SenseInside is an innovation project that was spun-out from the SFI DigiFoods to verify the commericalisation potential of the early miniaturized NIR prototype developed in DigiFoods.
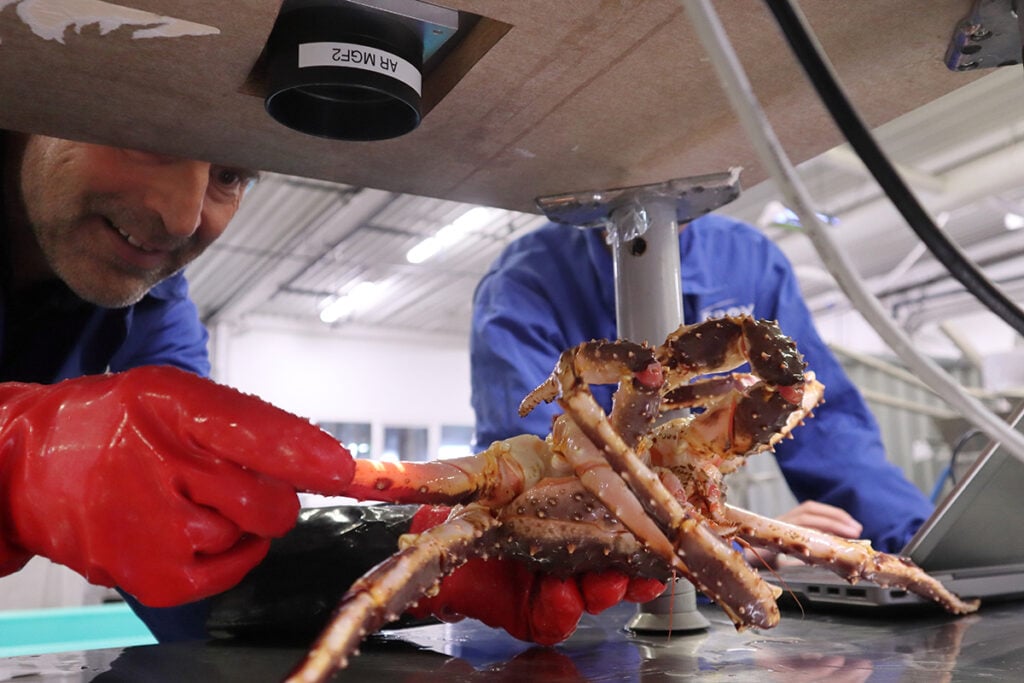
The miniature NIR instrument has been tested on crab meat content, strawberry and tomato sweetness, dry matter in clip fish, and fat content in salami sausages.
To conduct commercialization studies, Jens Petter Wold from Nofima and Jon Tschudi from SINTEF made an eventful journey to Lerøy in Kjøllefjord in September 2024, which is about as far north as you get in Norway. After two attempts with troublesome weather and technical issues with the plane, the determined DigiFoods team finally made it to Kjøllefjord in September 2023.
In 2023, our initial attempt to visit Kjøllefjord was aborted when the flight was sent back to Tromsø just before arriving in Hammerfest, due to technical problem. This time, in 2024, Jens Petter was unlucky enough to have his flight to Mehamn aborted due to strong sidewinds before it was redirected to Tromsø. The next flight out of Tromsø was also unsuccessful and resulted in a diversion to Kirkenes, overnighting in a hotel before flying to Lakselv and driving 4 hours to Kjøllefjord, almost 24 hours later than scheduled. Jon, who had luckily arrived a day earlier, waited patiently (a tourist for the day😉) for Jens Petter to arrive with the SenseInside instrument so that the commercial trials could be conducted. The bigger SmartSensor prototype, against which SenseInside was to be compared, had luckily arrived by Hurtigruta a few days early just before that route was also cancelled due to the weather!
So why didn’t Jens Petter and Jon give up and return home? How important is it for us to involve industry in our research? And how was the trip in the end?
Raimo Sørensen and his team at Lerøy did an excellent job preparing for our visit, and we managed to set up all the instrumentation, and complete all the scheduled experiments
Comparing two instrument prototypes
Lerøy had ensured that we had a sample set of 20 live king crabs, which they had manually checked to ensure varying meat content, and they had prepared a place for us to do our work. But even more importantly, they got involved in the testing – they assisted us in handling, labelling, and measuring the crabs, and even got trained up so that they could control one of the prototype instruments.
All the crab legs were measured with two instrument prototypes, SmartSensor and SenseInside. This interactive research is invaluable for us in DigiFoods, making all the difference when building a business case around the newly developed measurement technology.
One thing is measuring the crabs and knowing that the instrument works – that is something we can do ourselves in the lab with the right samples – but it is an entirely different experience to see how end-users in industry handle the crabs, how they managed to guide the legs to the instrument, how they would use a mounted instrument versus a handheld instrument, and what type of software interface is intuitive for them. And of course, the availability of live crabs is, of course, much greater in Finnmark than in the lab at Ås.
King crabs with varying meat content give good sample distribution for the tests
The return journey to Oslo was also eventful, with the flight from Mehamn being cancelled, but it did mean that Jens Petter and Jon got to spend a nice evening in Kjøllefjord, followed by a scenic drive to Lakselv the next day! After the commercial trial, Lerøy slaughtered and cooked all the crabs, froze them and shipped them to Nofima for follow-up reference measurements in the lab. This allowed us to determine the performance of the instruments.
At Nofima, all the legs were cut at the correct position and inspected for meat content. This manual observation was then compared with the measurements made by the instruments at Kjøllefjord.
Lerøy had done a good job in providing us crabs with varying meat content, so we had good sample distribution for the tests. We could verify that the new smaller SenseInside actually performed slightly better than the bigger SmartSensor. And that performance was in line with earlier promising studies.
New technology need to address industrial demands
Designing technology that is useful in industry places different demands on us researchers than just showing that something can be measured. This journey from demonstration to product involves understanding how an instrument measures, its user friendliness, its size and shape, and the industry’s willingness to pay.
These are all essential inputs to get technology across the ever-looming valley of death. We are now working on securing more funding so that we can get more industrial involvement. This funding would allow us to take a Minimum Viable Product (MVP) approach, which will build on what we have done in our commercial trials at Kjøllefjord in 2024 and Brødrene Sperre with clipfish in 2023.
By building a product that is not expensively over-engineered in an echo chamber, we aim to send out an early product, or MVP, with just enough features to be usable by early-adopter customers who can then provide feedback on how the final product should look, feel and function.
We are also looking for new applications and markets to test this on, as this increases attractiveness from a business perspective. We need to show that this product development track is worth investing in and get a better idea of how many we can realistically sell in the future. We also have an ongoing patent process to protect the uniqueness of the technology, which is also essential for commercialization.
We have high hopes for SenseInside – there is still work to do, but we believe in its potential!